The Iron Furniture Guide
Forging & Casting, Pros & Cons, and Maintenance Tips
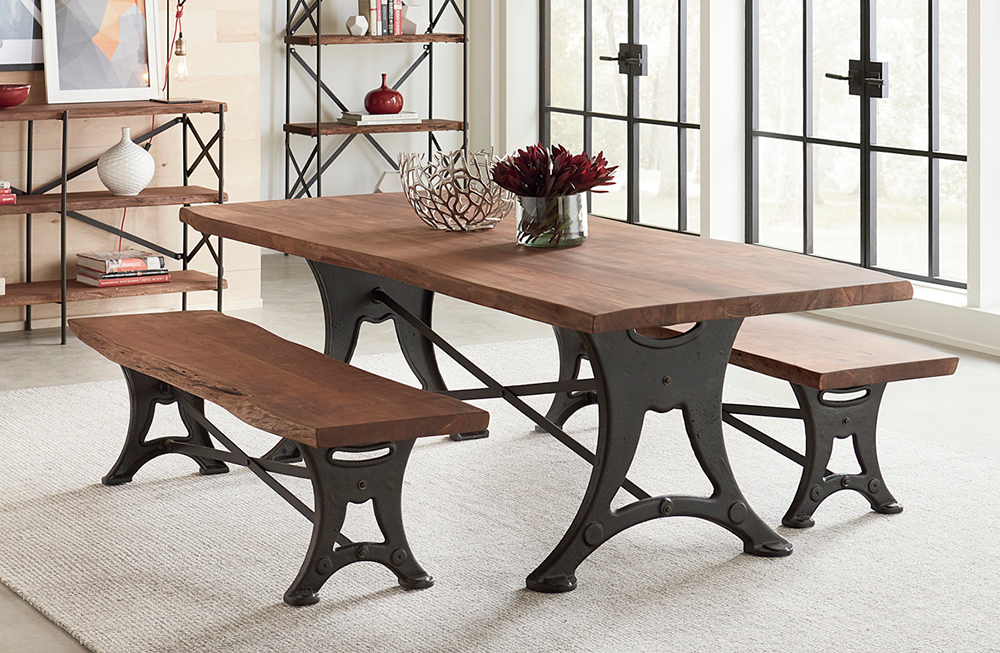
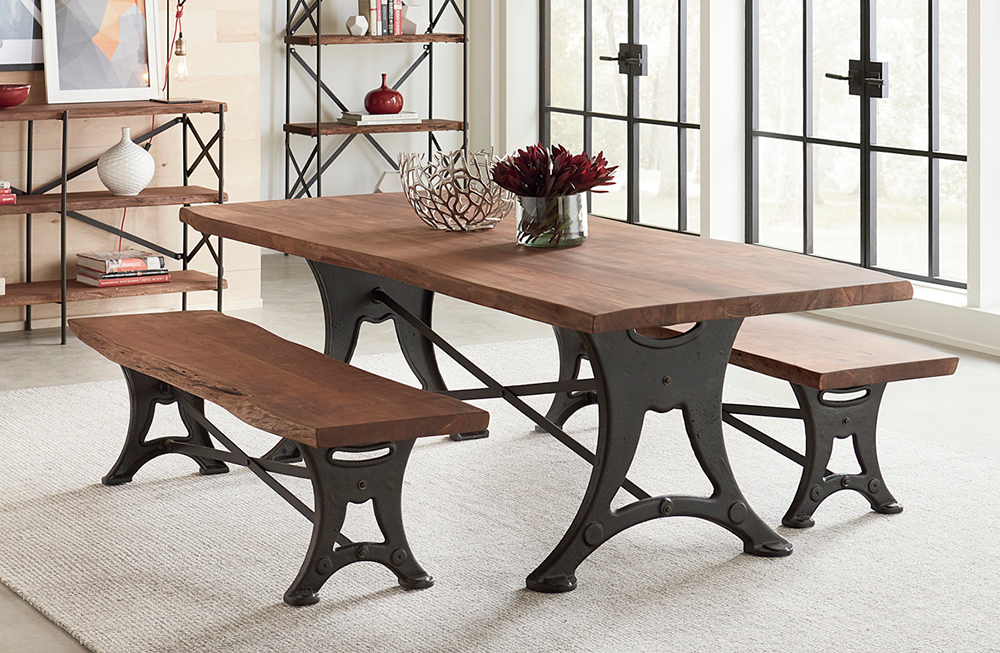
Why do We use Iron for Furniture?
Iron is our choice metal for many of our pieces. Not only is iron a great material due to its characteristics - it can be produced in an eco-friendly and sustainable manner as well. This article covers everything about the iron we use - from the types of iron and their sources to maintenance tips for our bases.
Strength
Cast iron is actually a carbon-iron alloy, while forged iron is made up entirely of iron. The carbon added in the cast iron process increases the molten iron's strength when cooled, while forging iron allows for the retention of the iron's natural grain structure, leading it to be a stronger material for furniture than any other alloy on the market, including bronze and aluminum alloys.
Design
Iron has a naturally cool and neutral color. This makes it incredibly versatile as the color palette matches a variety of styles. The main styles that influence our designs for iron furniture are mid century modern, rustic modern, and industrial modern, as the elements from these styles compliment the natural colors coming from the materials we use.
Cast Iron
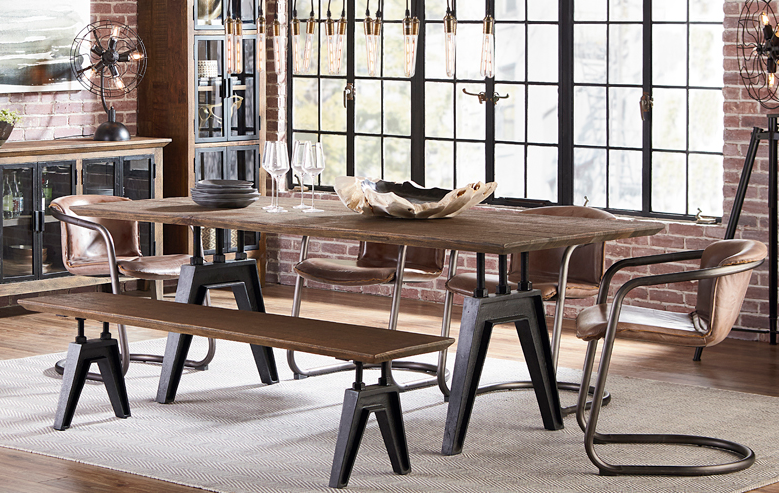
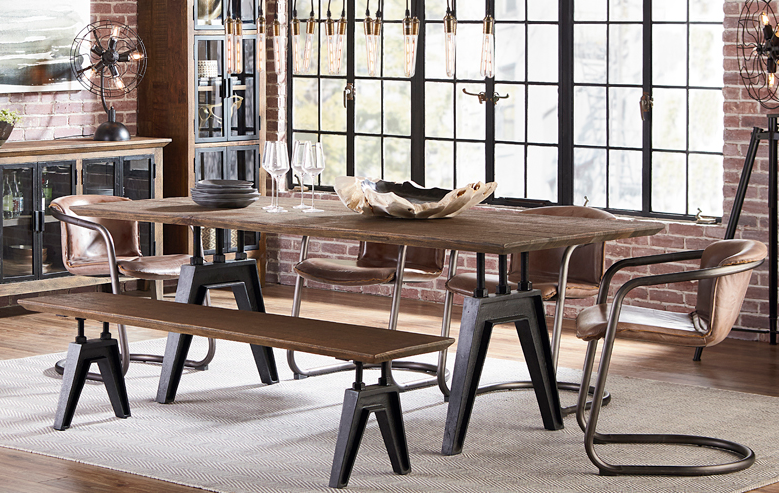
Sand-casted cast iron is a type of iron formed by pouring molten iron into a cast, letting the metal cool & harden, then extracting the cooled piece to for finishing.
- Durable - Cast iron is the choice material for many automotive parts for a reason - it can withstand a ton of wear-and-tear.
- Tried-and-True Technique - By using a system that has been refined by dozens of generations of craftsmen, we not only pay homage to those who came before, but also guarantee that the piece will be of the highest quality.
- Eco-Friendly & Sustainable - After sand casting, the remaining scrap can be melted for use in the creation of the next piece. This ensures that nothing goes to waste
First, a pattern is created. The pattern is a replica of the desired end product and will be placed into the sand in order to form a mold. Pattern making is one of the most important parts of the mold casting process, because this is where the liquid-hot iron will be poured.
To ensure that the material is spread evenly throughout the piece, a gating system is set up. A gate system typically consists of a pouring cup and tunnels, or "gates", which funnel the molten iron into the mold cavity.
Once the pattern is created in the sand and the gates are finalized, the iron scraps are then heated to their melting point and poured into the mold. Afterwards, the piece is left to cool and harden before removing from the sand.
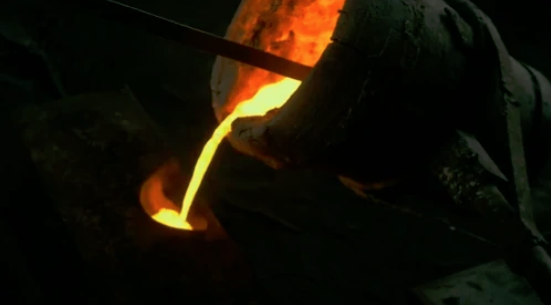
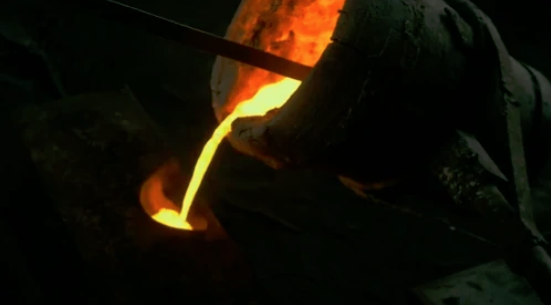
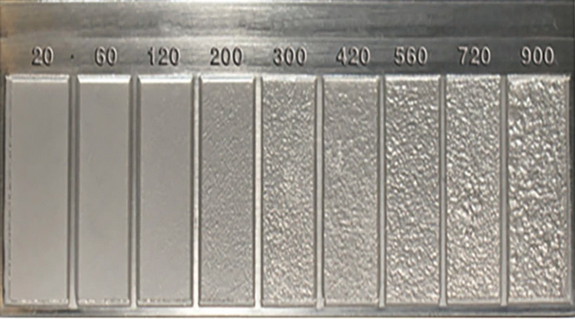
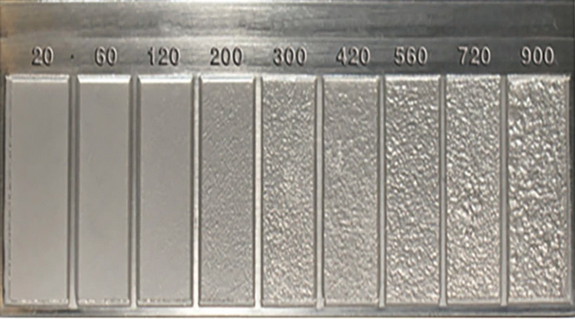
Once the cast is extracted from the mold, it is subjecting to a finishing process. Finishing the cast iron removes the impurities from the piece and protects it from corrosion.
During this process, the surface of the cast is first filed down in order to produce a smoother texture while also removing impurities in the metal.
After filing the metal down, the piece is then either painted or sealed with a clear coat, depending on the piece. This is done in order to protect the piece, making it corrosion resistant.
Pros
Perfectly Imperfect - Since every piece is casted and finished by hand, there are minor imperfections and variations between every piece. These imperfections provide the uniqueness inherent in handcrafted items, without compromising the structural integrity of the piece.
Rustic Result - Much like metalwork found in a barn or farmhouse, our cast iron bases exude a hardy, yet welcoming charm.
Easy Maintenance - Iron is an incredibly strong material that, when finished, is corrosion resistant and requires minimal maintenance beyond occasional dusting.
Cons
Lower Strength than Forged Iron - Since the iron is melted down and poured into a mold, the molecular structure changes. Because of this, cast iron is strong but stiff, giving it little flexibility.
This isn't an issue for furniture - this difference is only noticeable when the iron is bearing a load weighing more than 3 tons.
Forged Iron
Some of our other iron bases consist of iron pieces that are first forged, then welded together to form the final product. Forging is the process of using heat and physical pressure in order to give form a metal into a desired shape. We typically do this by hand, using a hammer and anvil - in accordance with traditional techniques.
Strong, yet Flexible - The forging process retains the iron's molecular structure, resulting in a piece that has superior strength when compared to casting.
Industrial Aesthetic - Forged bases are simple and strong, which are core principles of industrial modern design.
Eco-Friendly - Because iron forging is a relatively simple process when compared to other ironworking processes, there are less rejected products. This reduces the amount of scrap generated from the manufacturing process, This makes forged iron not only stronger than many other types of processed iron, but more eco-friendly as well.
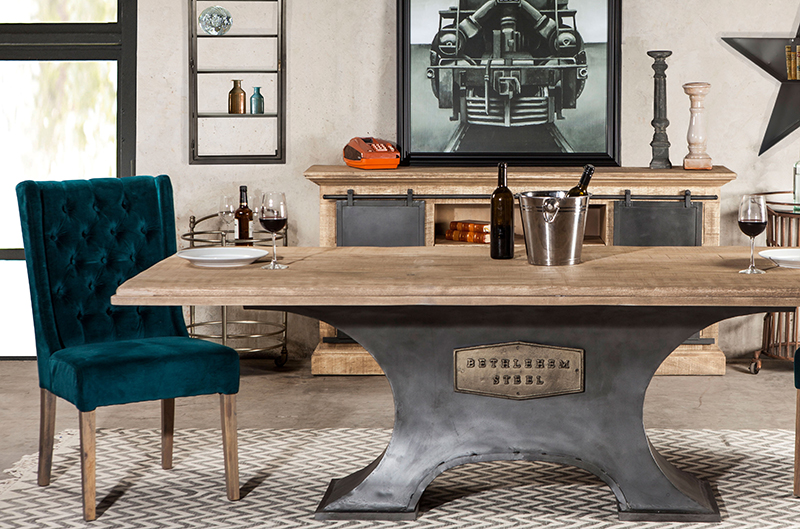
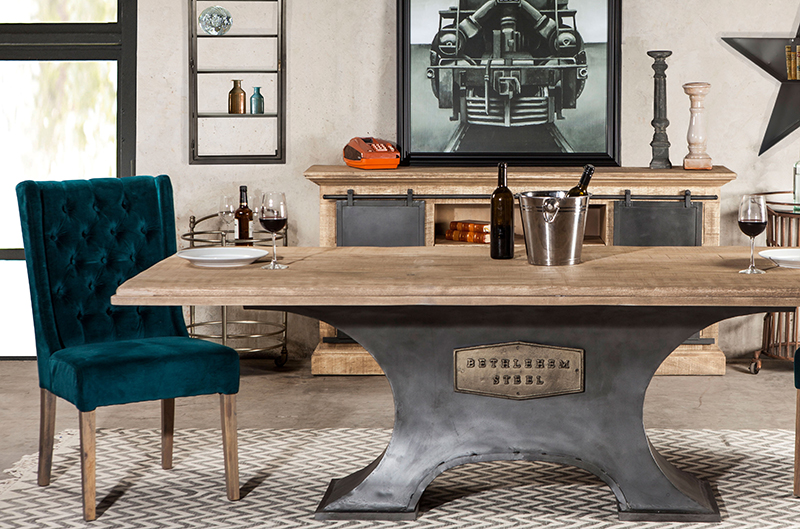
Heating
Before pressing the metal into shape, it is typically necessary to heat the metal to the point where it is malleable but not molten.
This process is accomplished by using a forge. Forges use fuel and air in order to heat the metal but too hot that it melts it (2500° F or 1371° C).
Shaping
Once the iron is properly heated, it can then be molded into shape using a hammer & anvil.
There are several techniques used for shaping forged iron:
Drawing Out - The process of using force to increase length while also making it thinner
Upsetting - Applying force at the end of a piece in order to add volume or width
Peening - The process bending metal in a specific direction
Quenching
After a metal is shaped, it must then be cooled. To accomplish this, the metal is placed in a quenching bucket.
Quenching liquid contains a unique mixture of mineral oils that harden the iron, as well as minimizing the the chances of warping or cracking.
4 step process
- Blasting - Blasting removes any dirt, grime, or corrosion. All of our forged bases are sand-blasted.
- Prepping - Prepping consists of applying a metal prep chemical solution to remove surface impurities, clean off any lingering debris, and make the piece corrosion-resistant.
- Powdering - Once the piece is prepped, the coating is then applied. This is done through electrolysis, in which the metal object is positively charged in order for the powder to be attracted to it and bond well during the next stage. Please note that our powder coating is rated for indoor use only. Placing our pieces outside may damage the piece's coating, making it vulnerable to corrosion.
- Curing - This is the process of heating the powder-coated piece in order to strengthen the chemical bonds between the coating and the metal. Typical curing temperature ranges from 250°F to 400°F are required for the powder to heat up enough to bond.
Pros
Extremely Strong - Forged iron is less porous than cast iron since it is not melted prior to shaping. Because of this, the end product with superior strength.
Simple & Sleek - Since forged iron pieces tend to have simpler shapes with sleek, straight edges, These pieces lend themselves well to modern fusion designs. The geometric shapes and simplistic nature of the piece perfectly fit modern design principles.
Cons
Limited Sizes - The forging process is best suited for smaller pieces. Larger pieces are simply too big to fit on an anvil, which is why sand casting is the preferred method for large pieces, such as consoles or cabinets.
Limited Shapes - More intricate and complex bases are better suited for casting, as hand-forging has limited accuracy when it comes to fine details.
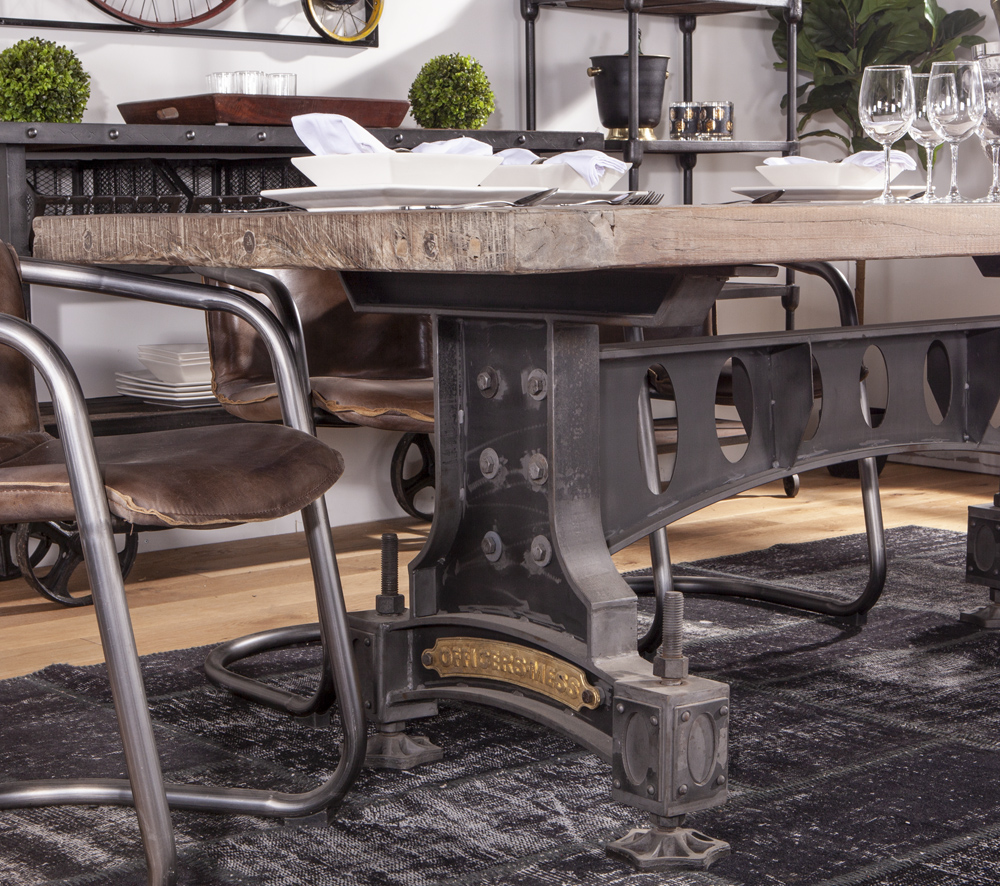
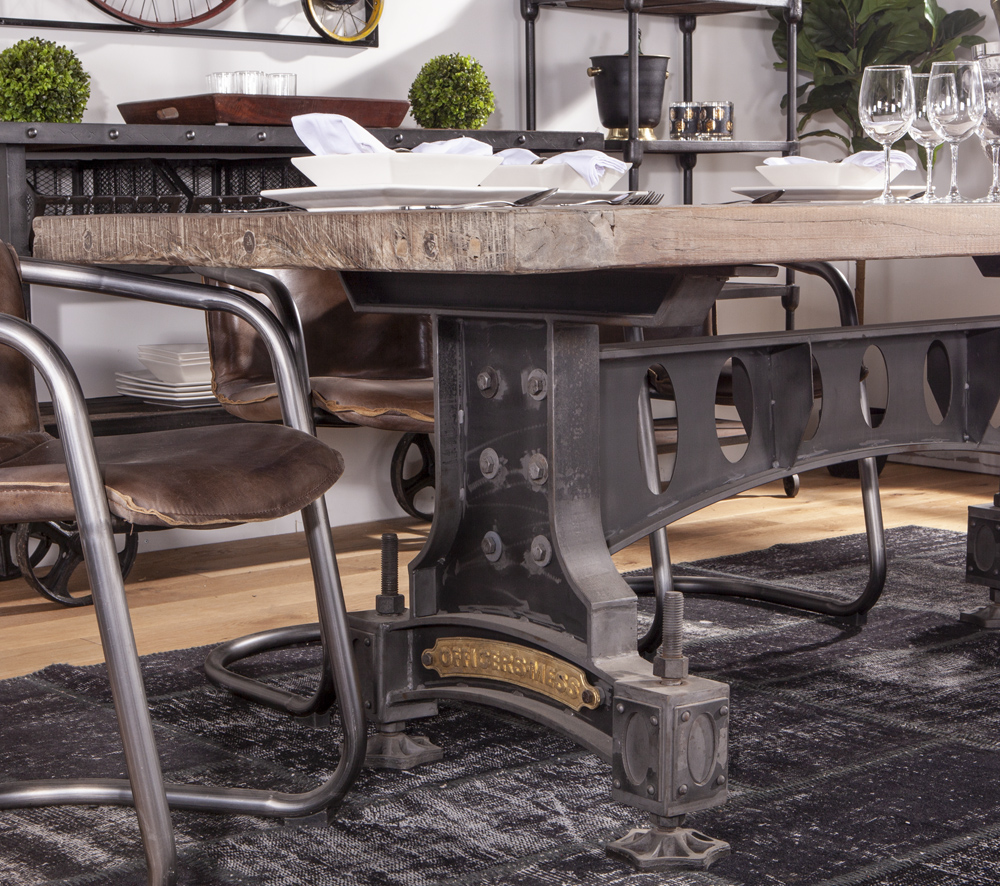
Maintenance
Both cast and forged iron are extremely durable, corrosion-resistant, and strong. They require almost no maintenance outside of periodic cleaning.
Here's some tips for keeping your cast and forged iron clean:
- We recommend dusting your base once a week
- If something spilled, wipe it off with a rag or sponge soaked in warm soapy water
- Avoid using harsher chemicals like bleach, as this will wear down the finish
- For additional protection, you can apply a light coating of non-abrasive car wax to protect from sun damage